Spreaders - cold and hot rollers
Cold Roller Spreaders
Thanks to the production needs of the market, Bimas has been able to develop a technology tailored to every need thanks to our experience on the field. We are able to fulfil artisan work as industrial work according to the customer’s requests. The range of the cold spreaders starts with model TF1-300 used as an example to glue beams, and ends with model TFP4QM designed for the plywood sector. Below you will find a description of various models of Bimas machinery with the specific field of usage.
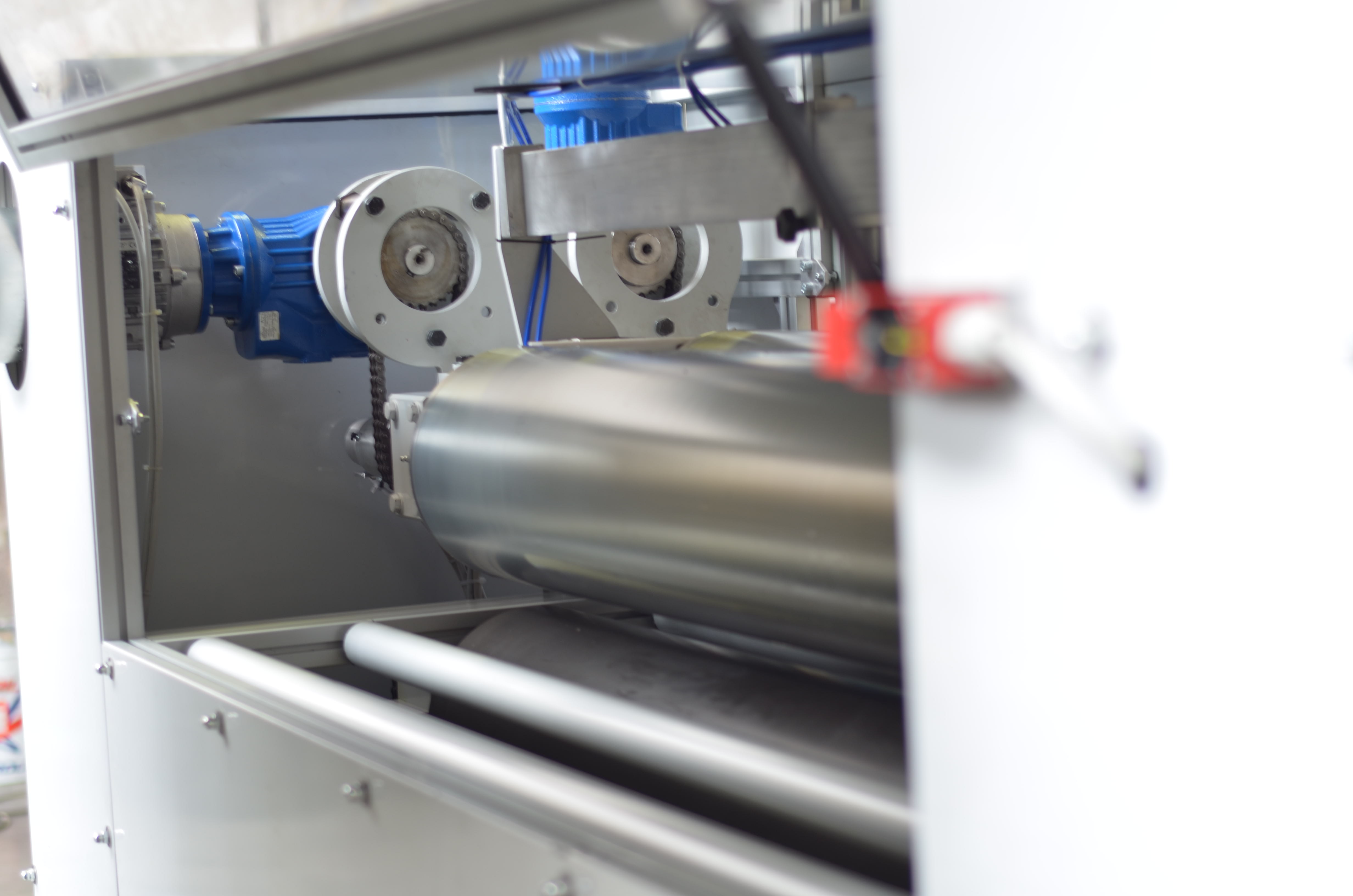
TF1 - 300
This spreader was designed for carpenters that work in artisan field. A simple and all around machine suitable for applying vinyl adhesives on glulam and beams. This machine can be customized with many optional such as pressing roller mounted on a higher detachable frame opposite to a lower reel, as a mechanical converter and motorized rollers and free rollers of special length suitable for the type of manufacture to develop, these are a part of the optional that can be built on the machine.
Data Sheet | |
Roll Width | 300 mm |
Diameter gluing roller | 135 mm |
Thread roller | Typical for each Job |
Working Height | 800 mm |
Power Electric Motor | 0.18 KW |
Transfer lenght free roller, input and output | 400 mm |
Speed gluing Roller | 25 mt/min |
TF2 - 300
Designed to spread both sides of the board with vinyl adhesive. The amount of adhesive is controlled by a bowl with a rectified lip to guarantee the precision of the amount in time. The machine is thought to be placed on the working surface; it can also be mounted on a specific base and introduced in existing production lines. The optional are the same listed for the TF1 – 300; mechanical converter and motorized rollers and clutches of special length suitable for the type of manufacture to develop, these are a part of the optional that can be built on the machine.
Data Sheet | |
Roller Width | 300 mm |
Diameter Gluing Roller | 135 mm |
Thread Roller | Typical for each job |
Working Height | for counter; base on request |
Power Electric Motor | 0.18 KW |
Transfer lenght free roller, input and output | 400 mm |
Speed Gluing Roller | 25 mt/min |
TF2
The TF2 range is designed for a working surface from 400 to 1600 mm; they are spreaders for a more dynamic ant continuous production than the TFS series. They are built on a stronger mechanic and the engine that moves the gluing rollers is more powerful. The quantity of glue control system introduced in the lower series is the same also for the TF2 series satisfying the need of a precise work. The possibility to work with many types of adhesives is assured by the many types of compounds that can be developed daily in the laboratory. The amount of vulcanized rubber on the reel permits the regeneration of the reel for several times. On request certain parameters of the machine such as speed or working passage can be managed mechanically and electronically thanks to specific control systems. The washing system, manual or automatic (installed on request) offers the possibility to save time and to operate in a clean area. The machine can be paired with a cooling system that makes it an all around machinery that can fulfil many needs for different types of productions. Rotating wheels or extraction line wheels can be installed to better use the working area for maintenance or production. The highest working performance can be granted (if required) by fitting adhesive dispensers (SAM) or bi-component (SAB). Safety is guaranteed by electromechanical (sometimes also electronic) systems that fulfil the safety requirements of the machinery.
Model | Widht Roller | Ø Roller | Speed Roller | Height transition Working | Power Electric Motor | Working Height |
TF2-400 | 440 mm | 185 mm | 18 mt/min | 0-150 mm | 0.37 Kw | 800 mm |
TF2-600 | 640 mm | 185 mm | 18 mt/min | 0-150 mm | 0.37 Kw | 800 mm |
TF2-1000 | 1040 mm | 185 mm | 18 mt/min | 0-150 mm | 0.37 Kw | 800 mm |
TF2-1300 | 1340 mm | 185 mm | 18 mt/min | 0-150 mm | 0.37 Kw | 800 mm |
TF2-1600 | 1640 mm | 185 mm | 18 mt/min | 0-150 mm | 0.75 Kw | 800 mm |
TF4S
This range is dedicated to the need of precision and the timing are the parameters to follow in relation to the amount of money to invest. The mechanical features and the dosage of the adhesive make this range reach the highest levels of quality. Two extra rollers are introduced in place of the bowl of the previous series, driven by a three-phase engine. The amount of adhesive is regulated by flywheels in techno polymer with gauges that move mechanical jacks installed on specific supports. The engine, specifically designed for this machine moves all four rollers. The side rails are in a material specific to the type of adhesive keep the machine always clean and tidy. The type of coating of the rollers and the dispensers follow the characteristics of the adhesive. The free rollers in stainless steel drive the object to the gluing rollers, a grill at the exit protects the worker. For smaller pieces it is possible to fit on the machine at the exit point motorized discs. As for the previous series it is possible to install machineries for adhesive dispensers, single (SAM) and bi-component (SAB). An automatic washing system for the rollers can also be installed. Safety is important for Bimas, all the electrical systems are controlled by electromechanical and electrical devices as stated by the machinery user guide.
Models | Width Roller | Ø Gluing Roller | Ø Batching Roller | Speed Roller | Height Transition Working | Power Electric Motor | Height Working |
TF4S-1300 | 1340 mm | 210 mm | 185 mm | 20 mt/min | 0-150 mm | 1.1 Kw | 800 mm |
TF4S-1400 | 1440 mm | 210 mm | 185 mm | 20 mt/min | 0-150 mm | 1.1 Kw | 800 mm |
TF4S-1600 | 1640 mm | 210 mm | 185 mm | 20 mt/min | 0-150 mm | 1.1 Kw | 800 mm |
TF4M
Bigger than TF4S, the TF4M is the top of the range in cold reel gluing for vinyl adhesives and urea glue. This machine has two engines fitted before the gluing rollers. The two engines guarantee higher precision and reliability over a long term. The amount of adhesive is regulated by flywheels in techno polymer with gauges that move mechanical jacks installed on specific supports. In the BASIC VERSION the free rollers in stainless steel drive the object to the gluing rollers, a grill at the exit protects the worker. The machine can be customized with many optional such as motorized rollers at the entrance of the machine and motorized discs at the exit when dealing with smaller objects. If an higher precision is requested an electronic control system can be fitted for positioning the dispenser rollers with brushless engines and high precision jacks. The machine is operated through a control panel with a CPU that manages the entire system. The side rails are in a material specific to the type of adhesive keep the machine always clean and tidy. The type of coating of the rollers and the dispensers follow the characteristics of the adhesive. As for the previous series it is possible to install machineries for adhesive dispensers, single (SAM) and bi-component (SAB). The perforated dispenser rollers and paired with a cooling system (GF3000 – 5000) is an optional that can be fitted when using an adhesive that requires low temperatures. An automatic washing system for the rollers can also be installed. Safety is important for Bimas, all the electrical systems are controlled by electromechanical and electrical devices as stated by the machinery user guide.
Model | Width Roller | Ø Spreader Roller | Ø Batching Roller | Speed Roller | Height Transition Working | Power Electric Motor | Height Working |
TF4M - 800 | 840 mm | 250 mm | 210 mm | 20 mt/min | 0-100 mm | 1.5 kw | 900 mm |
TF4M - 1300 | 1340 mm | 250 mm | 210 mm | 20 mt/min | 0-100 mm | 1.5 kw | 900 mm |
TF4M - 1400 | 1440 mm | 250 mm | 210 mm | 20 mt/min | 0-100 mm | 1.5 kw | 900 mm |
TF4M - 1600 | 1640 mm | 250 mm | 210 mm | 20 mt/min | 0-100 mm | 1.5 kw | 900 mm |
TF4M - 1800 | 1840 mm | 250 mm | 210 mm | 20 mt/min | 0-100 mm | 1.5 kw | 900 mm |
TF4M - 2000 | 2040 mm | 250 mm | 210 mm | 20 mt/min | 0-100 mm | 3.0 kw | 900 mm |
TF4M - 2200 | 2240 mm | 250 mm | 210 mm | 20 mt/min | 0-100 mm | 3.0 kw | 900 mm |
TFP4DM e TFP4QM
These type of spreader are designed for plywood and MD. The TFP4DM has two engines that drive the spreading rollers and the dispenser rollers; the TFP4QM has four engines one for each reel, spreader and dispenser. The rollers can be maximum 3600 mm. The machine is in steel and cast iron. The spreading reel has a diameter of 400 mm and the dispenser reel of 320 mm, this guarantees a perfect spreading of the adhesive. If an higher precision is requested an electronic control system can be fitted for positioning the dispenser rollers with brushless engines and high precision jacks. The machine is operated through a control panel with a CPU that manages the entire system. The machine can be upgraded with mechanical and electronic optional that can improve the production quality; RULLI PRESSORI, electrical frequency converters, motorized discs, washing system are some examples of what can improve the machine. The perforated dispenser rollers and paired with a cooling system (GF3000 – 5000) is an optional that can be fitted when using an adhesive that requires low temperatures. As for the other series the type of coating of the rollers and the dispensers follow the characteristics of the adhesive. It is possible to install machineries for adhesive dispensers, single (SAM) and bi-component (SAB). Safety is important for Bimas, all the electrical systems are controlled by electromechanical and electrical devices as stated by the machinery user guide.
Model | Width Roller | Ø Spreading Roller | Ø Batching Roller | Speed Working | Height Transition Working | Power Electric Motor | Height Working |
TF4PDM-1400 | 1440 mm | 400 mm | 320 mm | 25 mt/min | 0-100 mm | 8 kw | 950 mm |
TF4PDM-2000 | 2040 mm | 400 mm | 320 mm | 25 mt/min | 0-100 mm | 12 kw | 950 mm |
TF4PQM-1400 | 1440 mm | 400 mm | 320 mm | 25 mt/min | 0-100 mm | 8 kw | 950 mm |
TF4PQM-2000 | 2040 mm | 400 mm | 320 mm | 25 mt/min | 0-100 mm | 12 kw | 950 mm |
TF4PQM-2400 | 2440 mm | 400 mm | 320 mm | 25 mt/min | 0-100 mm | 12 kw | 950 mm |
TF4PQM-3000 | 3040 mm | 400 mm | 320 mm | 25 mt/min | 0-100 mm | 12 kw | 950 mm |
TF4PQM-3600 | 3640 mm | 400 mm | 320 mm | 25 mt/min | 0-100 mm | 12 kw | 950 mm |
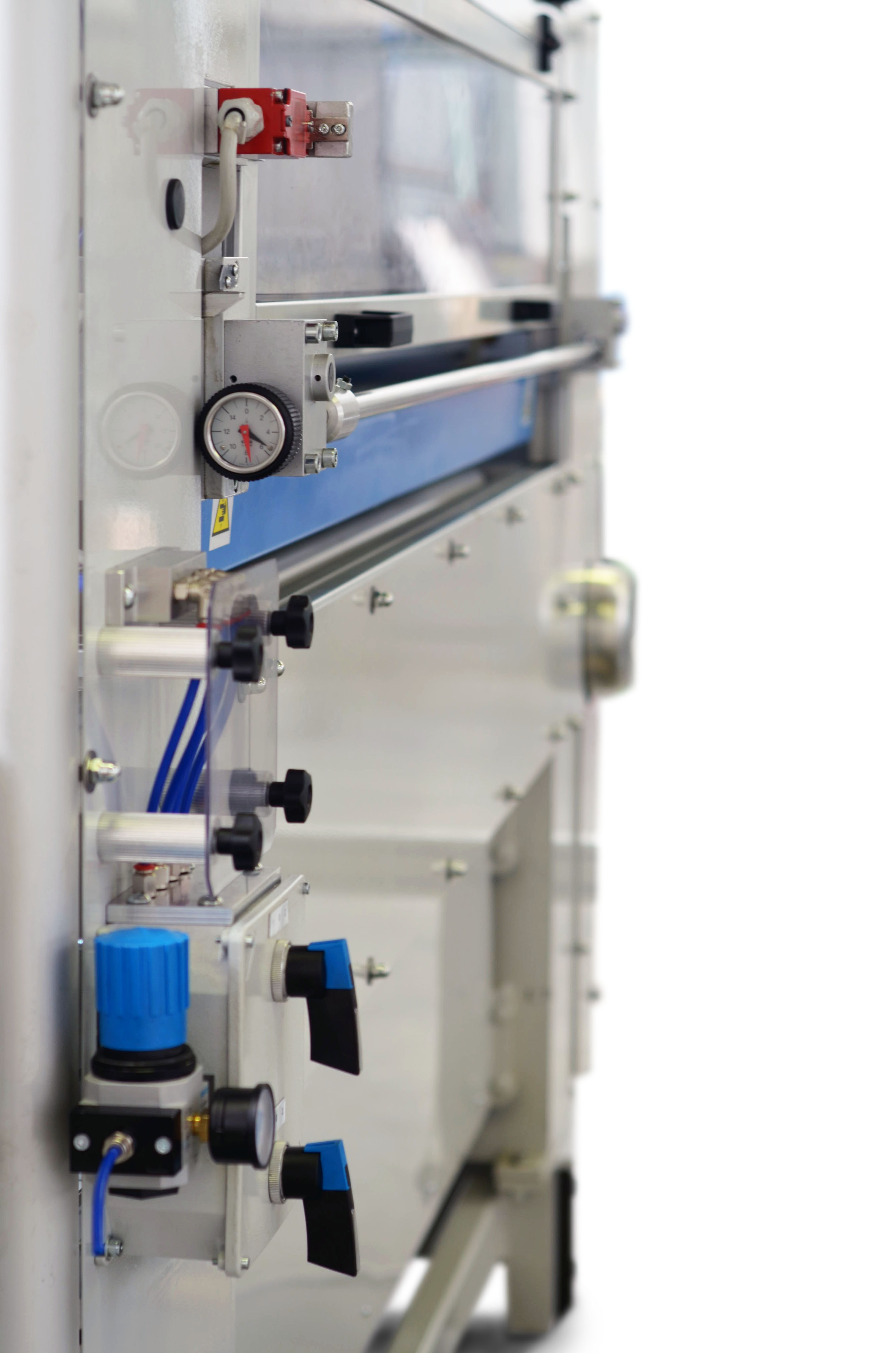
Hot Roller Spreaders
TC is the range of Bimas Engineering designed for hot melt adhesives. The machine can be built in many ways, and can be managed by a dedicated APP. The machine can have three or four rollers allowing the glue spreading on one or both sides of the panel. On top of each reel a gear motor controlled by an electrical frequency converter (if requested) can be fitted. The rollers can be heated separately and can be coated with silicone for high temperatures or with hard chrome coating. A specific diathermal oil is used as thermal fluid that allows a precise temperature control and an homogeneous heat. To control the heat special probes immerged in the oil are used to control the electric system. The side rails are in Teflon and fixed on a stainless steel plate; their capacity is guaranteed by pneumatic cylinders that maintain the pressure and optimize the wear. The side rails are easily removable. The machine can be fitted with automatic glue dispensers linked to the machine through heated pipes. An extractor fan can remove the hot air from the working area. Safety guards in polycarbonate provide safety from accidental interference and also help containing the heat produced by the rollers. The machine is PLC managed and the worker operates it by a coloured TOUCH SCREEN that can manage the great part of the working procedure.
Since the machine is designed for high precision spreading over a long term, we can fit on request by the customer an electronic/mechanic system for the centesimal regulation of the dispenser reel. Thanks to brushless engines and encoder it is possible to manage through PLC also this important feature. It is also possible to upgrade the machine with the following optional:
- Electrical frequency converter on every reel
- Automatic positioning of the higher spreading reel
- Adhesive proof treatment on the lower driving reel, entrance rollers and safety grill
- Motorized entrance and exit rollers for smaller objects
- Central rails to reduce the working surface
- Wheels for an easy positioning of the machine
- Stainless steel bowls
The machinery is built according to CE standards and requirements.
Model | Widht Roller | Ø Spreading Roller | Ø Batching Roller | Power Electric Motor Spreading Roller | Power Electric Motor Batching Roller | Power heating for each roller | Height Working |
800 mm | 840 mm | 250 mm | 215 mm | 1.5 kW x 2 | 0.37 kW x 2 | 5 kW | 900 mm |
1400 mm | 1440 mm | 250 mm | 215 mm | 1.5 kW x 2 | 0.37 kW x 2 | 5 kW | 900 mm |
1600 mm | 1640 mm | 250 mm | 215 mm | 1.5 kW x 2 | 0.37 kW x 2 | 5 kW | 900 mm |
1800 mm | 1840 mm | 250 mm | 215 mm | 1.5 kW x 2 | 0.37 kW x 2 | 5 kW | 900 mm |
2000 mm | 2040 mm | 250 mm | 215 mm | 1.5 kW x 2 | 0.37 kW x 2 | 5 kW | 900 mm |
2200 mm | 2240 mm | 250 mm | 215 mm | 1.5 kW x 2 | 0.37 kW x 2 | 5 kW | 900 mm |